When Topring audits a facility, we’re looking for solutions or alternatives to help our clients with three key aspects: safety – efficiency – performance.
In this case study, our solutions focus on safety and efficiency.
Context of the case study
Manufacturer of artificial respirators
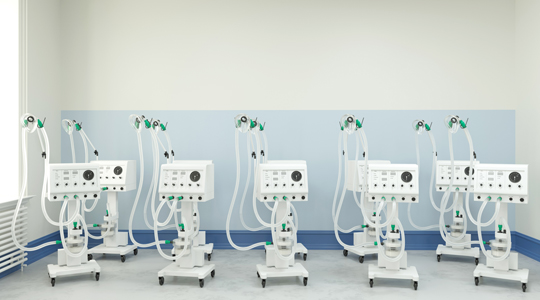
The Canadian government ordered 40,000 artificial respirators for the anticipated second wave of COVID-19.
When the COVID-19 pandemic occurred last spring, the Canadian government ordered 40,000 artificial respirators for redistribution to the country’s hospitals. The goal was to better prepare Canadian hospitals for the anticipated second wave of COVID-19. Public health authorities fear that the next surge will be significant enough to overwhelm Canada’s health care system. For the time being, hospitals have enough artificial respirators. The new order is intended to increase existing stocks.
Health Canada selected five authorized manufacturers for these orders. One of these manufacturers hired Topring to supply a specialized component: the preset pressure regulator. This part is meant not only to produce thousands of new respirators, but also to develop improved equipment for Canada, the U.S., Mexico and countries in South America, Europe, the Middle East and Africa.
Purpose: To help the Government of Canada fight COVID-19, save lives and, by the same token, contribute to Canada’s economic recovery.
The manufacturer chose Topring because of our ability to:
- Deliver on the mandate’s technical criteria.
- Customize our service to the situation, whether for engineering, project/product management or consultants.
- Prioritize the project, since developing a new product involves 24/7 interactions about design, quality standards, production capacity, technical specifications, certifications, and so on.
- Supply several thousand parts within a short time.
Challenges and solutions
The challenges for artificial respirator manufacturers:
If a patient experiences complications from the 2019 coronavirus disease (COVID-19), this may lead to respiratory distress, which means they will need help breathing. All medical ventilation devices (commonly referred to as ventilators or artificial respirators) must meet specific standards and carry certifications as people’s health depends on their reliability. The device’s main role is to provide the lungs with artificial ventilation.
A respirator is made up of two elements:
- A respiratory diffusion unit that reproduces the inhalation/exhalation cycle
- A graphic interface that controls respiratory flow
Challenge #1 Precise, constant pressure
To be effective, a respirator must be properly regulated. The device must supply a precise, constant flow of air to assist the patient’s lungs. Pressure that is too high or too low can seriously impact the patient’s health. Every component of an artificial respirator is chosen based on the small margin of error and the reliability of each component.
Manufacturers meet specific standards. When it comes to public health, there’s no room for error. That’s why every manufacturer must meet high quality standards and the margin of error must be as small as possible.
Challenge #2 Limited space
From a technical perspective, the medical ventilation device should be as compact as possible. Careful attention must be paid when choosing every component. Because everything must fit together in the device as compactly as possible, the weight and size of each part is calculated. Naturally, each one must also meet the standards and certifications imposed by public health authorities.
Manufacturers apply two practical criteria. The device must be mobile so that health care workers can easily move it around. The device must take up very little room near the patient, since there is usually limited space.
Challenge #3 Meet demand in very little time
It usually takes a long time to develop and produce a new respirator. Given the high demand for this type of device, the project involved a much shorter timeframe for design. The multiple components from numerous sources had to make it through a complex approval process before production began. With the global health crisis, the deadlines imposed by the government required the manufacturer to shorten its regular lead time. The ventilator project was a success because the manufacturer was able to deliver a high volume of ventilators in just a few months.
Solution: The preset regulator
One of the manufacturers authorized and selected by Health Canada to manufacture artificial respirators chose to use Topring’s preset oxygen regulator.
The preset regulator is the ideal solution for oxygen supply systems. It delivers accurate, tamper-proof and constant pressure at the outlet, with a minimal margin of error. Compact and lightweight, it can be used for medical equipment, respiratory and anesthetic devices, as well as food and beverage conservation.
Features and benefits:
- Made with FDA-approved Grivory materials and stainless steel
- Tamper-proof preset pressure for optimal performance
- No risk of incorrect pressure
- Highly reliable
- More compact and 3 times lighter than standard regulators
- Service free – no adjustment needed
- Easy to mount on all oxygen supply systems
- Wide range of preset pressures, from 15 to 120 PSI
- Still reliable after 10 million cycles
- No pressure gauge required
How it works
1. When the regulator receives oxygen, pressure pushes it through the open valve, from supply to use.
2. If the preset pressure at the outlet is less than the spring force, the spring holds the piston, which opens the valve.
3. When the preset outlet pressure is reached, the force of the oxygen pressure pushes the piston into the valve, closing the regulator.
4. When the oxygen is consumed, the valve opens and oxygen again begins to flow from supply to use.
The Topring experience
When you use a Topring pressure regulator, the tolerance for the margin of error is so small that pressure remains stable across devices. As a result, every artificial respirator can safely perform its role of reproducing the inhalation/exhalation cycle to safeguard patient health. In addition, because the pressure regulator is so compact and light, the weight and size of the artificial respirators are unaffected. Finally, Topring was able to deliver the high volume of units ordered and meet the manufacturer’s tight deadlines. Choosing Topring to supply one of its ventilator parts made a big difference and likely contributed to the manufacturer’s success.