Air networks are an efficient way to distribute compressed air to multiple locations within a building. Depending on the piping material, air networks can offer multiple advantages such as modularity, quick installation and durability, as well as reduced maintenance and operating costs.
Table of Contents
1. Compressed air applications
2. Planning
3. Material
4. Project costs
5. Certifications
6. Topring piping systems
7. Installation
8. Air quality and treatment
9. Maintenance and air leakage
10. Safety
11. Training
12. Technical support
The multiple applications of compressed air
Compressed air is an important source of energy for many industrial applications. It is considered the fourth most used process after electricity, natural gas and water. It is used to operate various types of pneumatic tools and equipment. It offers a variety of advantages.
The numerous application of compressed air:
- General industry - Machines and equipment, pneumatic tools
- Machine shop - Use of blow guns for cleaning and cooling of parts
- Body shop - Paint application that requires a large amount of air (clean and dry)
- Garage - Use of tools that require high air volume (impact tools)
- Tire shop - Use of air and nitrogen for inflation
- Construction contractors - Harsh work environment (product quality)
- Handymen, artists and other professionals
Advantages of using compressed air:
- Lower operating costs than electricity
- Clean energy
- Adjustable precision of use (possibility of regulating air volume and pressure)
- Less physical space required for installations
- Reduced risk of fire (no sparks)
- Centralized maintenance at the compressor (for the motor)
- Occupational health and safety: lighter tools reduce fatigue and injuries
Planning and design of an air network
The planning stage of a compressed air system ensures optimal equipment efficiency, reduced operating costs and improved workplace safety.
Compressed air requirements vary depending on the application and there are many configuration possibilities. Each project requires a unique approach.
Where do you start your project? How can you be sure that you are not overlooking anything and that the network you are setting up is optimally adapted to your industry’s needs and requirements?
Here are six important questions to consider before starting an air network project:
- What type of application will the compressed air be used for?
- How much compressed air will be required?
- Where are the pneumatic tools and equipment to be located?
- Will the system be closed loop or linear?
- Are there any air quality requirements to be met?
- Who will be performing the installation?
The Topring team has put together an in-depth blog post on How to design a compressed air system.
The different piping materials
Piping systems for compressed air systems can be made from a variety of materials. Before making a choice, the characteristics of each system should be considered.
Depending on the type of material, it will have a different impact on efficiency, leak tightness, durability, adaptability, maintenance, installation, and overall cost over the long term.
Black or galvanized steel
Black or galvanized steel has long been used for piping systems. Conventionally, it is the one that is selected by default, due to its low cost, among other things. However, this does not take into account its characteristics and its impact on the system.
Over time, steel oxidizes. Rust forms, breaks off and causes particles to contaminate the entire network. The inner surface of the pipes becomes rough, causing pressure loss and turbulence.
In the case of galvanized steel, oxidation is slower, but still inevitable. New pipes are hot-dipped galvanized and therefore coarse textured on the inside.
Steel is a very heavy material and more difficult to work with. Installation can be long and complex. Each fitting requires cutting the tube and adding at least two threads. These steps make the system difficult to modify once assembled. Threading also involves the use of cutting oil, which will eventually contaminate the pipe.
The screw-in system with sealant is the least airtight method available in the industry. This results in air leakage and therefore increased operating costs.
Copper
Copper is a material that is used extensively in the medical gas industry. Some pharmaceutical industries require it as a matter of habit since it meets high air quality standards. In some situations, it is the only material that meets the standards set by these industries.
Copper is more expensive than black steel. It is heavy to handle and requires soldering to connect. During installation, this results in a complex job site requiring important safety measures to be respected. Soldered connections make it difficult to modify once the network is in place.
Stainless steel
Stainless steel is a material that is resistant to corrosive elements and oxidation. However, it is heavy, expensive and even more difficult to thread than black steel. Therefore, even in industries where there is a high use of chemicals, such as the paper industry, it is rarely selected.
Aluminum
Aluminum was introduced into the market a few years ago due to a drop in the cost of the raw material.
Aluminum pipes are smooth, which reduces pressure losses throughout the network. The fact that aluminum does not rust eliminates all issues related to oxidation.
Unlike other materials, aluminum is very simple to install and easy to handle. The tubes do not require any threading or welding and the method of assembly ensures optimal sealing. Aluminum tubing is three to four times lighter than steel tubing of the same size. In most cases, two installers in a boom lift are required to install a steel tubing network, whereas only one is needed to install an aluminum tubing system. This translates into a large saving in time and labour, which has a major impact on the cost and completion of the project.
The Topring team has put together a blog post with 5 reasons to choose an aluminum compressed air pipe.
What is the cost of a compressed air network?
Calculating the cost of an air network project is complex as it is made up of a multitude of variables. All aspects of the network must be included in the equation. In general, they are divided into four cost categories:
- Cost of materials
- Installation costs
- Operating costs
- Maintenance costs
The cost of each of these categories is influenced by the choice of material, the quality of air and volume required, the frequency of use, the length of the network and the airflow rate, all of which determine the diameter of the pipework.
Cost of materials
The cost of materials covers the compressor room equipment, including the compressor up to and including air handling solutions; the main piping system and its connections; and the points of application, including the air preparation equipment and the distributors.
Installation costs
Installation costs are determined by the time and labour required. Both are directly influenced by the quantity, weight and size of materials, the method of assembly, and the accessibility of the location where the network is installed.
Operating costs
Basically, the operating costs consist of the energy bill to run the network. This is related to the amount of air produced, which in turn varies according to air consumption and air loss.
Maintenance costs
Maintenance costs include periodic servicing of some of the system’s components, one-off repairs, and the labour required to perform the service.
Comparing steel with aluminum
This graph illustrates the influence that the choice of pipe material has on the overall cost categories of an air network project. The data displayed are for similar projects: in the first case using steel, in the second using aluminum.
The graph shows the importance of evaluating the costs as a whole. It is essential to consider not only the purchase price of materials, but also the installation cost, as well as the ensuing operating and maintenance costs.
Certifications
There are a number of different types of certification for piping systems. When selecting parts for a compressed air system, it is important to consider all the certifications obtained for each product.
In Canada, several provinces may require a Canadian Registration Number (CRN) for certain parts of a compressed air system that uses a pressure greater than 15 PSI. Validation of Canadian Registration Numbers (CRNs) is strongly suggested for all pipes and fittings during the planning of an air network project.
Other certifications that may be important in determining the desired system are: ISO 9001.2015, ISO 8573-1.2010, UL 94 Standard for Safety of Flammability, NSF H1 Classification, ASME B31.1 and ASME B31.3, and many others. The manufacturer can inform you about the different certifications that apply to its products.
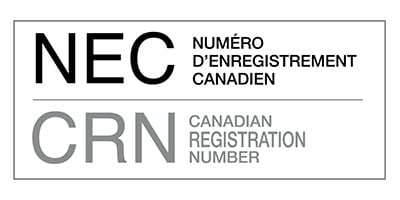
Registered under the Canadian Registration Number (CRN)
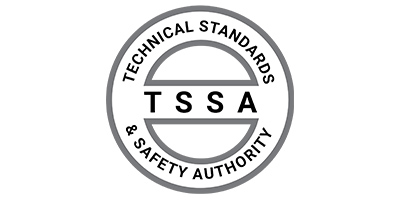
Registered with Technical Standard & Safety Authority (TSSA)
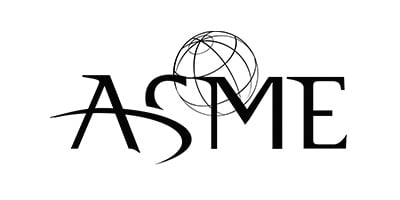
Meet the requirements of ASME B31 / ASME B31.1 / ASME B31.3
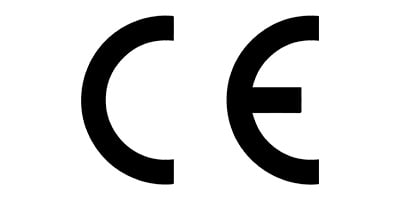
Complies with the European Pressure Equipment Directive (PED) 2014/68 / EU
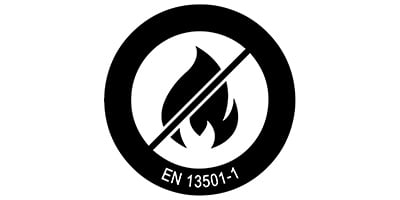
Complies with STANDARD 13501-1: 2018 fire protection standard
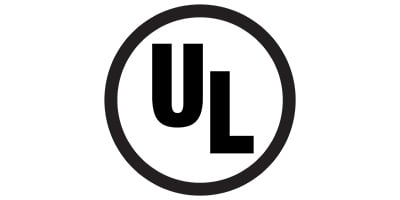
Complies with the flammability safety standard UL 723 -ASTM E84 UL 94 HB
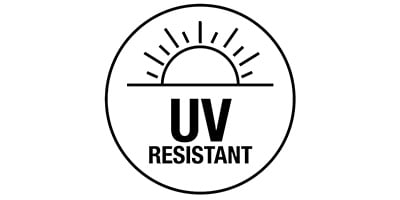
UV resistance
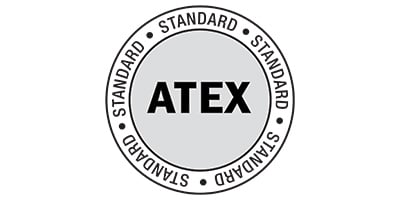
comply with the ATEX Directive: 2014/34 / EU Zone 1 & 2 - 21 & 22
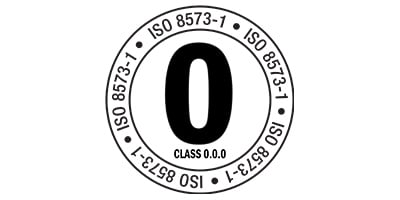
Conform to ISO 8573:2001 & 2010 Classe 0.0.0
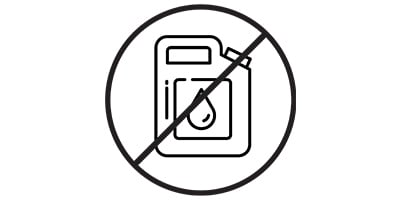
Oil free
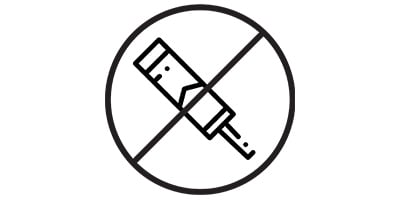
Silicone free
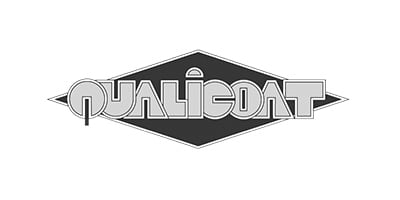
Comply with the QUALICOAT label, which guarantees the quality of the painting process, the chemicals used, the finish and the resistance of the aluminum tubes.
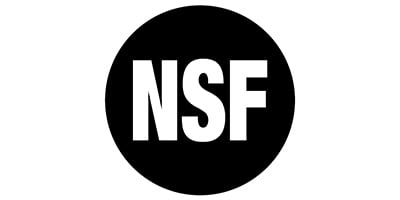
NSF-H1 certified lubricant for the food industry
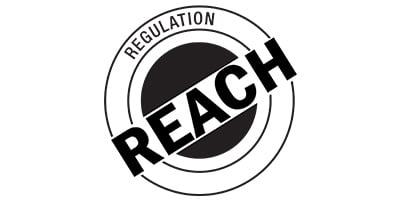
Compliant with REACH regulation EC1907/2006
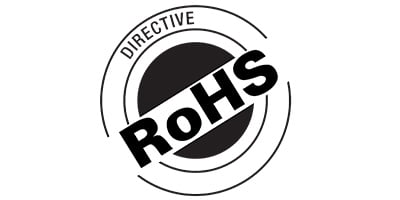
RoHS compliant
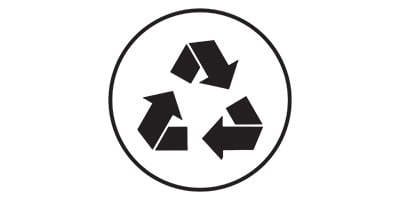
Recyclable
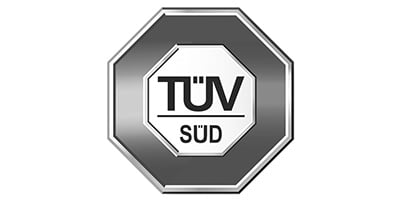
Quality system ISO9001-2015 certified
PPS piping system
Topring has developed one of the most innovative and efficient compressed air systems available, with the added benefit of being 100% aluminum. The PPS range has all the qualities required to meet the most demanding needs of the many industries that rely on the use of compressed air.
PPS piping and fittings have been designed through years of research and development to overcome the shortcomings of other products.
In comparison to the vast majority of choices on the market, all Topring piping and fittings are made of aluminum and have a Canadian Registration Number (CRN).
To find out more about Topring’s range, visit pps.topring.com.
Installation of an air network
All piping systems have their own particularities. The installation methods differ whether it is steel, aluminum or two products using the same material.
The main differences are in the process of connecting the system, securing the tubing, and the labour and tools required.
As explained earlier, products that can be installed quickly offer an economic advantage over the total cost of an air system project. Aluminum systems stand out because of their light weight and the fact that they can be connected without threading or welding.
Compressed air treatment and quality
Air treatment plays a critical role in the performance of the air system, regardless of the quality of the piping used. Air that is not properly treated can adversely affect the application due to moisture, contaminants or temperature fluctuations in the piping.
In order to maximize the full potential of the air system, it is essential to review your air quality requirements. Several solutions are available to achieve the desired air quality, such as water separators, air filters, refrigerant air dryers, condensate traps and oil/water separators. The combination of one or more of these elements will ensure that the air is at the right temperature and that it is sufficiently dry.
To learn more about air handling, read the blog post "The 6 key steps to an efficient compressed air system."
Maintenance and air leaks
Maintenance of a compressed air system is essential to ensure the efficiency, performance and safety of the system, tools and pneumatic equipment. Regular maintenance of the system limits the costs associated with air production and distribution and ensures energy efficiency for years to come.
Over time, the use of the system causes normal wear and tear on many filters, hoses and tools. Sometimes repairs are the best option. However, most of the time, a replacement part is needed. Find out how to repair a hose or how to service a filter/regulator/lubricator.
Vibration and thermal variations can also cause a seal to be broken, which can lead to air leaks. Learn about the different methods of detecting compressed air leaks here.
Condensate can also accumulate in tanks and drop legs. Purging these impurities is important to prevent them from causing damage and reducing the efficiency of the system. Click here to find out more about the different types of condensate drains.
Consequently, keeping your system in good condition requires that you periodically check several system components to ensure that they are in good condition. Topring has developed a 3-step checklist to facilitate the inspection of an air system.
Safety
Safety should be paramount in all industries. Air systems can be hazardous when they are poorly designed and improperly used by their operators.
Various solutions are available to prevent accidents and to ensure the ongoing efficiency of the system.
For more information on compressed air safety, see the blog post "Compressed air safety: Prevention is the watchword".
Training
Topring has produced a 20-minute video training course that outlines the main principles of air network design. Several topics are covered:
- The different materials used in air systems
- Air requirements
- Selection of tube diameters
- Network design
- Use of slopes
- Thermal variations
- Mounting
- Vibration
This course highlights the importance of properly planning a network project and explains the basics. Get free access to the compressed air system planning workshop.
Technical support
Each air network project is unique. The larger the project, the greater the level of complexity. This is why the advice of an expert is an asset in guiding the design and execution of a plan.
Topring provides the opportunity to speak with a technical advisor to help guide you through your project successfully.