Don´t oversee, ignore, or postpone the important safety issue in the workplace. Make it a part of your morning routine to check on all systems and installations….be diligent!
In this article we focus on due diligence in occupational risk and safety.
What does ''due diligence'' mean?
Due diligence is not about having a thing (a policy, a system, procedures, checklists, etc.) it’s about doing a thing. Demonstrating due diligence is about being diligent. And diligent is defined as «showing persistent and hard-working effort in doing something». So, demonstrating due diligence is focused on doing; it is an activity thing.
Being diligent requires administrators to go and look, question, and understand what is going on in their business. It required administrators to enter the workplace and actively interact with the people conducting the work. It requires administrators to understand about (not just know about) the risks that they (actively) know are present in the business and that people are engaging with. The administrators understand about the risks because they are diligent (persistent and hard-working) in their risk understanding activities. They are diligent in their active pursuit of these activities which include active questioning, active listening, and active understanding.
Further, demonstrating due diligence is also about being able to (actively) confirm that «what is going on», is what they agree is «what ought to be going on. And they know this because they are active in finding out from these same people what those most appropriate methods might be; including actively ensuring «as best they can» that these same people have the necessary resources (skills, knowledge, well-being, support, equipment, etc.) to discern and manage the risks.
Demonstrating due diligence is also about being active in knowing when the unexpected happens. Importantly, it is about stopping and reflecting (as individuals and collectively) on what has happened (good and not so good) and paying active heed to experiences and learning from them.
Due diligence is about risk intelligence as much is it about systems. It requires that you:
- Identify all workplace hazards
- Implement all necessary preventive measures
- Communicate appropriately to all necessary personnel
Injury and Illness Prevention Programs: what are they?
According to OSHA’s white paper on Injury and illness Prevention Programs, these programs are flexible, common-sense, proven tool to find and fix hazards before injuries, illnesses, or deaths occur. They must include 6 core elements:
- Management leadership
- Worker participation
- Hazard identification and assessment
- Hazard prevention and control
- Education and training
- Program evaluation and improvement
Why are Prevention Programs so important?
According to OSHA, in the US, more than 12 workers die on the job every day – that represents over 4,500 a year. Every year, more than 4.1 million workers suffer a serious job-related injury or illness. Businesses need an enhanced focus on prevention to bring these numbers down. Let’s also not forget about the societal costs or injuries and illnesses. In the US, workplace fatalities are estimated at $40 billion / year. Occupational illnesses (condition that results from exposure in a workplace to a physical, chemical or biological agent to the extent that the normal physiological mechanisms are affected, and the health of the worker is impaired) are evaluated at 60 000 deaths per year and 850 000 new illnesses per year.
What are the proven benefits of Prevention Programs
- Transform workplace safety and health culture
- Reduce injuries, illnesses, and deaths
- Lower workers’ compensation and other costs
- Improve morale and communication
- Enhance image and reputation
- Improve processes, products and services
Implementing injury and illness prevention program could also reduce injuries by 15 to 35%, save $9 billion to $23 billion per year in workers’ compensation costs and reduce indirect costs.
Top Benefits of Effective Workplace Safety Programs
Hazard Identification
Hazard identification is a risk assessment practice that aims to identify and record safety risks and work hazards to ensure the safety of workers and personnel. Hazard identification is usually done:
- when new processes, equipment, and/or machinery are introduced into the standard workflow;
- before each shift;
- in the performance of work;
- during formal or informal inspections; and
- after incidents occur.
It is the employer’s responsibility to inform, educate, and train their employees about workplace hazards. It is paramount to ensure a safe and healthy environment not just for employees but for clients as well. Early detection of hazards and implementing safety practices will help the business in achieving its goals and many other benefits.
Prevent numerous work-related injuries and illnesses;
1. Improve compliance with laws and regulations;
2. Reduce costly repairs and unexpected damages;
3. Improve employee engagement, productivity, and efficiency; and
4. Boost overall business operations.
How to Identify safety hazards?
Failure to spot hazards can often lead to serious injuries and dangers in the workplace.
All safety and health programs must consistently identify and assess hazards to ensure that all workers are safe and protected.
A hazard identification procedure is done through a collaborative effort of employers and workers.
A step-by-step procedure could be as follows:
1. Gather information about existing hazards that are likely to be present in the workplace. Browse free hazard identification templates online.
2. Perform regular site walkthroughs to identify new hazards.
3. Review accidents and near-miss logs to further investigate the root causes and program shortcomings.
4. Identify similar trends across all incidents, illnesses and hazards recorded. Also, consider hazards that are present on non-routine jobs.
5. Determine the level of risk, significance, and frequency of each hazard to know which needs to be prioritized.
Hazard Control Measures
In effectively controlling and preventing hazards, the National Institute for Occupational Safety and Health (NIOSH) developed the hierarchy of controls to guide workplaces in implementing the most feasible and effective control solutions. There are 5 types of controls that can be applied, each intended for a specific purpose:
Hierarchy of Controls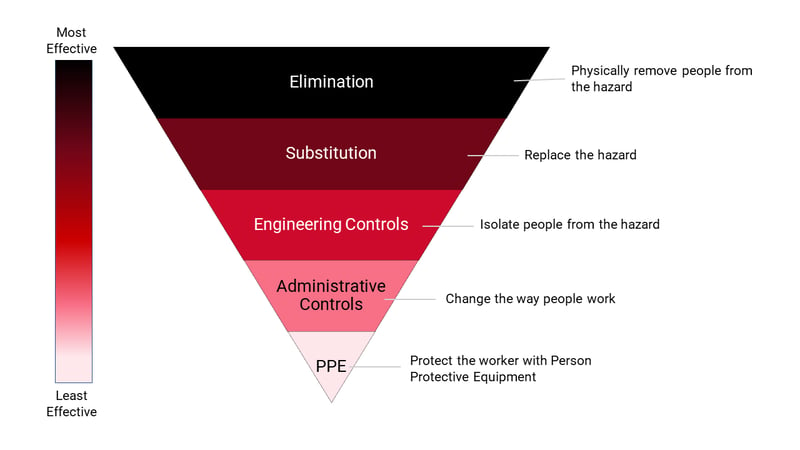
There are many free hazard checklist templates online. Here is an example of a due diligence checklist: