Accidents caused by improper use of compressed air are common. Safe and appropriate use of products for compressed air reduces the risk of injury and improves overall productivity. We have grouped our security solutions according to the problem to which they relate. Take stock of your solutions and consult our Safety Solutions Catalogue to complete your compressed air system.
Table of contents
How to clean with compressed airHow to prevent hose whips
How to reduce noise exposure
How to avoid accidental start-ups
How to make your workstation ergonomic
How to prevent tripping
How to protect the air system from overpressure
How to dispose of condensates
12 safety rules to remember
Links of interest
How to clean with compressed air
First and foremost, a few precautions to take when using compressed air to clean.
- Wear safety glasses to prevent particles from irritating or damaging your eyes.
- Inspect equipment (e.g., ensure debris is not lodged inside the blow gun)
- Never point a jet of air directly at a colleague
When we talk about cleaning with compressed air, you have 3 possibilities:
- Cleaning of equipment by blowing
- Cleaning of equipment by vacuum
- Body cleaning by vacuum
⚠️ Warning
It is illegal to use a blow gun to remove debris from clothes or bodies. This is a very common practice and yet it is prohibited by law (learn more about cleaning regulations). The air jet pressure presents many risks of personal injuries, such as:
|
|
Cleaning of equipment by blowing
A compressed air system in a plant normally operates between 80 and 120 PSI. Most pneumatic tools require a working pressure of 90 PSI. This is the case with compressed air blow guns.
A blow gun is considered safe when the static pressure at the point of blockage is less than 30 PSI. Why? Because the chances of injury are virtually zero. See the article Are You Familiar With the 30 PSI Standard for Blow Guns? to learn more about this rule.
Static pressure below 30 PSI
If you are using a blow gun or air gun, make sure that the tool has a nozzle that reduces the pressure under 30 PSI if the end of the nozzle becomes blocked. If the nozzle is blocked, the air stream is diverted to the side openings, reducing the static pressure.
Here are three examples of nozzles that have this feature.
The venturi-type nozzle draws in ambient air through the side holes. The displacement of the air is then amplified up to 25 times. Therefore, this type of nozzle offers unparalleled efficiency in addition to protecting you during a cleaning operation. The comparison below between a standard nozzle and a venturi nozzle shows this well. The cans are quickly taken down with the use of a venturi nozzle, while a standard nozzle requires a little more precision.
Startip nozzles, as their name suggests, have star-shaped tips. Like venturi-type nozzles, they produce a concentrated jet of air for maximum efficiency. Both nozzles offer the same safety feature that allows air to escape through the radial holes if the tip is blocked, allowing the static pressure to remain below 30 PSI.
Flat nozzle blow guns are specially designed to deliver a powerful jet of air to a specific location. They are ideal for cleaning workbench surfaces, machinery, equipment, and areas requiring a low volume of noise. Use a flat nozzle to clean chips and splinters, clean parts and equipment, blow, dry, and move dust.
Output pressure at 0 PSI in case of obstruction
Some models of safety blow guns have an internal valve that completely stops the air jet in case of nozzle obstruction. The output pressure is automatically 0 PSI if the tip of the nozzle becomes blocked. The valve re-activates to let air in as soon as the tube is clear. This type of blower is therefore the safest on the market.
Reduce pressure at tool air inlet or point of application
There are also safety solutions to make a non-restricted blow gun that is not equipped with a nozzle to reduce pressure under 30 PSI or an internal mechanism that completely stops the air stream in case of nozzle obstruction.
A 29 PSI preset pressure regulator installed at the tool fits directly into pneumatic tools and blow guns. It provides a constant outlet pressure, regardless of the inlet pressure. It prevents overpressure and excessive air consumption (which reduces energy costs).
A 29 PSI preset pressure regulator installed directly into the compressed air system provides accurate and consistent output pressure. Regardless of the inlet pressure, it is not possible to tamper with the mechanism. It prevents dynamic pressure loss by limiting the overconsumption of air, which promotes energy savings.
Beware of dislodged particles
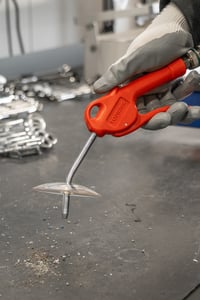
When cleaning with blow guns in confined areas, debris can fly back into the face, causing serious injury. That’s why for such operations, OSHA and other health and safety agencies require that you protect yourself effectively.
In addition to wearing safety glasses, which are highly recommended, you can equip the blow gun nozzle with a protective shield to protect you from dislodged particles flying back.
Some blow guns are equipped with a protective air screen: a small portion of the main air stream is deflected through the slots around the nozzle to form an air screen that will protect you from the blowback of debris and dust. In the event of nozzle obstruction, all airflow is diverted to the side openings and static pressure is maintained at less than 30 PSI.
Cleaning of equipment by vacuum
When cleaning equipment, it’s preferable to use suction. This is much better than blowing and even better than sweeping. Suction makes it possible to pick up large dry and/or liquid debris. It is therefore perfectly suitable for collecting a wide variety of waste, such as:
|
|
|
The vacuum barrel cleaner is powered by compressed air. Therefore, it operates without electricity, limiting the risk of explosion or fire caused by static charge. Using a vacuum cleaner also avoids blowing debris and thus eliminates any risk of debris flying back in the face of others or oneself.
The compressed airflow rate influences the suction performance. For best results, use a hose with a minimum inside diameter of ¾ inche and a high flow (high-throughput) quick coupler.
Body cleaning by vacuum
Since the law prohibits using compressed air to clean the body, use something with suction instead. Although blowing dislodges dust, it also involves blowing particles into the air, which inevitably contaminates the air you breathe. In the long term, exposure to contaminated air can cause respiratory complications and illnesses. Did you know that 3 out of 4 cleaning-related accidents are caused by particles being blown into the eye, despite wearing protective eyewear?
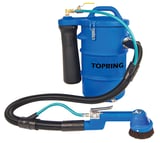
Cleaning units are a good alternative for cleaning the body since they have powerful suction. The brush is composed of an internal agitator that lifts particles from the surface and aspirates them efficiently. For maximum safety especially if you work in an industry that produces a lot of dust or other particles (e.g. sawdust, wood chips, and wood meal), equipping your workshop with a cleaning unit is a good investment.
Advantages and features of the personal cleaning unit:
- It does not emit a jet of compressed air, thus there is no physical risk.
- It has a standard filter (0.8 micron), HEPA filter (0.3 micron), or antistatic filter.
- It is ideal for removing particles stuck by moisture or sweat.
- It can be installed on a vertical surface to save space and is easy to maintain.
- It keeps the work environment clean.
- It is powered by compressed air. The absence of an electric motor eliminates the risk of sparks.
Vaccum guns are a smaller and less cumbersome solution. This type of vacuum can be used for both surface cleaning and body cleaning.
- They are easy to handle.
- They have powerful suction to collect debris.
- They are designed for heavy-duty use.
- They are powered by compressed air. The absence of an electric motor eliminates the risk of sparks.
⚠️Reminder: never use an air blow gun to clean yourself. ⚠️
How to prevent hose whips
When a fitting detaches from a pressurized flexible hose or when a pressurized hose ruptures, the flow of compressed air escapes uncontrollably. The hose then produces a whipping motion and can result in it hitting or whipping everything in its path. Projectiles or a hose in a whiplash motion is equivalent to a speed of 150 km/h, which can cause :
- Injury to nearby workers or bystanders
- Damage to parts in production
- Rising of dust from the floor
- Dispersion of particles in the air
Best Practices
- Never leave your hose lying on the ground as you could run over it with a forklift for example. It may wear out prematurely by repeatedly rubbing on the ground or, it could become damaged by pulling it if it’s stuck.
- Never let a 50-foot hose that is fully extended out of the hose reel to retract freely.
- Always make sure you have the right type of coupler plug with the right type of quick coupler (female and male compatible).
Securing air hoses
To prevent hose whips caused by an accidental hose disconnection, you can install a air fuse between the supply point (e.g., at the FRL outlet) and the air hose. The value of the air fuse is preset at the factory and configured to allow free passage of air during normal use of an air tool. If the air consumption exceeds the preset value of the air fuse, the internal piston immediately shuts off the compressed air supply. Once the breakage is repaired, a built-in bleed hole allows some air flow to escape. This automatically resets the air fuse.
Demonstration of a hose break with or without an air fuse:
Because of its process, the air fuse enforces two safety standards related to the use of air hoses:
"Any flexible hose exceeding 1/2 inch I.D. must have a safety device at the source of supply or at its connection point on the line, to relieve pressure in the event of hose breakage." OSHA Standard No. 1926.302(b)(7)
"Where a failure of a hose assembly or rigid plastic tube constitutes a whiplash hazard, it shall be restrained or protected by appropriate means, and/or a compressed air safety valve shall be installed." Standard ISO 4414-11 (5.4.5.11.1)
⚠️ Caution: Care must be taken when selecting an air fuse. The safety of the users and the proper operational function depends on it. Read the complete air fuse selection information before making a choice.⚠️
Quick couplers with zero pressure disconnection are also another way to prevent dangerous hose whips and accidental disconnections. When there is a disconnection, the pressure is vented downstream before the plug is removed. There are two types of connections available:
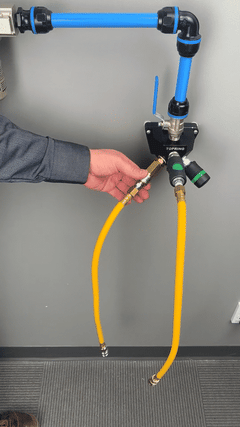
A two-stage disconnection system releases the downstream pressure, disconnecting the plug while it remains in the fitting. A manual action then releases the plug completely while the pressure is zero. For maximum safety, some fittings also require pushing the ring of the fitting back to reposition the butt in a straight line for removal. The butt should be held by hand until the hose is completely vented.
A similar one-touch disconnection mechanism is also available with some fitting models. With a single push of the button on the fitting, air pressure is cut off and automatically removed downstream. The plug is disconnected, but retained in the fitting. It can then be safely removed. For maximum safety, equip your air system with safe quick couplings with zero pressure disconnection.
See the article How to Choose a Quick Coupler for a guide to the coupling selection process.
Securing air hose reels
For maximum safety, equip your hose reels with an air fuse or, when purchasing, opt for a hose reel that comes with an air fuse.
If the air consumption exceeds the preset value of the air fuse, the air supply to the hose reel is immediately cut off by the internal piston of the air fuse.
Whiplash can also be caused by an automatic hose recoiling too fast automatic on a standard reel. If the hose is not retained by the user, the consequences will be the same as when a pressurized hose breaks or becomes detached.
For maximum safety, equip your reels with a slow-motion recoil device or opt for a reel that comes with one. This allows you to rewind the hose slowly and evenly.
How to reduce noise exposure
Excessive noise in the workplace is a hazard to workers' hearing. The impact of repetitive noise is often underestimated; however, it can cause lifelong disabilities. It is the costliest occupational disease in society. OSHA and other health and safety agencies have established standards for daily noise exposure limits to protect workers.
Noise exposure
In a factory or other work environment, noise levels do not add up, they combine. If two noise sources emit 80 dB, the measured exposure level will be 83 dB. The brain is unable to distinguish the strength of staccato sounds that assault the ear. Therefore, it cannot adapt to them. Repetitive noise is perceived as a continuous sound, which is why it is dangerous for hearing health when exposed to it for a long time. In Canada, the legally tolerated noise level is currently 85 dB. A daily exposure of 8 hours to a noise level exceeding 90 dB will eventually cause hearing loss. Hearing protection must be provided by the employer when the sound level exceeds the safe level.
Daily duration, in hours | 8.0 | 4.0 | 2.0 | 1.0 | 0.5 | 0.25 |
Exposure level in dB | 85 | 88 | 91 | 94 | 97 | 100 |
Source: CSST L.R.Q., c. S-2.1, r.19.01 Section XV, 131.
The reference level
The reference level is the maximum continuous noise level allowed during a full 8-hour shift.
Noise tolerance
To represent the noise tolerance level, the following diagram illustrates the severity of various noise levels with examples from everyday life.
Remember that it is continuous and repetitive exposure to a high noise level that makes a noise a threat to hearing health. 90 dB is the decibel level where increased exposure to noise can cause real damage to the inner ear and increase hearing loss.
Reducing noise at the source
Noise sources in plants vary by application and industry. Noise is present regardless of the power source used. To identify and measure them, most of the time it is enough to go from the biggest equipment to the smallest visually. Let's think first of the equipment, the big machinery and various industrial processes (ejection of parts, cleaning, drying, stamping, moulding...), then of the various tools used (rotary, percussion, to suck or eject air...), and finally, let's think of everything that comes from the smallest operation and handling (reel, balancer, forklift, door...). Whenever possible, focus on reducing the noise level at the source.
The use of compressed air blow guns
Air blow guns are used in many industries to clean, dry and dust work surfaces, as well as to eject and dry parts in a manufacturing process. However, they can produce high noise levels and contribute to occupational deafness.
Blow guns that emit less than 85 dB of sound (which is considered a low noise level and a standard required by most Canadian provinces) are called “silent”. Silent blow guns, therefore, help prevent and reduce the number of workers who become hearing impaired due to the use of compressed air.
A good alternative to a silent blow gun is to equip your spray gun with a silent nozzle. The noise level will then be reduced by up to 20%, without compromising the power of your spray gun. Ask your technical advisor for more information on this type of solution.
Industrial processes
One of the most harmful noises when using a compressed air system comes from the exhaust of pneumatic valves. As an example, a valve with ½ inches ports controlling a pneumatic cylinder at 3 cycles per second produces noise equivalent to a continuous level of 92 dB. Pretty noisy, isn't it, considering the allowable level is 85 dB?
A common solution is to use air mufflers to silently exhaust compressed air from air valves, air motors, and pneumatic impact tools. They muffle the air exhaust noise from pneumatic valves and help preserve hearing health in the workplace. As a guide, an air muffler reduces noise by up to 85%.
To cool and extend the life of tools, cold air guns with integrated silencers are an economical and efficient alternative. In addition to avoiding the use of coolants that could cause air contamination, their big advantage is that they have a low noise level.
How to avoid accidental start-ups
Unexpected pressurization of an air system can activate a tool or equipment suddenly and result in serious injury. Even when the air source is disconnected, there is still air pressure stored inside a tool or equipment. This is called residual pressure. The air does not bleed out on its own, you must let it out. If you don't, the accidental start-up of a tool or equipment could occur.
Releasing residual pressure
Residual pressure is the term used to describe the pressure stored inside a tool or piece of equipment, even if the compressed air source is disconnected.
Preset pressure regulators installed directly at the tool or between the quick coupler and the hose allow residual pressure to escape into the tool to prevent accidental activation of the tool after disconnection. They ensure a constant, preset pressure to the tool and no alteration of the mechanism is possible, regardless of the input pressure. This is an economical way to achieve the ideal tool pressure and save energy while increasing tool life. It makes it safe to use a non-restricted blow gun since the static pressure is less than 30 PSI if the nozzle is clogged.
Locking out equipment
Lockout is the practice of using a padlock or safety device with a padlock to secure a machine, valve, safety valve, or shut-off valve in the closed position. This allows for safe maintenance and prevents accidental start-up of the compressed air system. This is a standard regulated by OSHA to protect workers during maintenance operations (OSHA Part. 1910.147).
Lockout valve with locking handle are a 2-position, 3-way valve that exhausts downstream air when shifted in the closed position. They are used during maintenance procedures on equipment operating with compressed air (5 microns). These valves are installed in downstream air lines or individual compressed air systems.
- With their bright yellow color and red handle, their unique and conspicuous appearance makes them easily distinguishable from other air system components.
- A padlock can be inserted into the locking latch to lock the unit and restrict the supply of compressed air. This allows for safe downstream maintenance since it can be padlocked.
- They have a high airflow exhaust port.
Safety exhaust ball valves with locking handle are used to isolate sections of the piping system for repairs, tie-ins, expansions, and maintenance.
- They are only lockable in the closed position, which provides maximum safety while performing work.
- When the valve is in the "closed" position, residual air escapes through the exhaust port. When the valve is in the "open" position, a simple 90° rotation of the handle immediately cuts off the flow.
- The safety exhaust ball valve body includes a threaded (10-32 UNF) depressurized vent outlet that redirects the exhaust air and allows the muffler to be assembled to reduce noise.
Lockable exhaust shut-off valves for Filter/Regulator (F/R) and Filter/Regulator/Lubricator (F/R/L) units are installed directly on the filter components. They isolate the point of application from the rest of the compressed air system. The 3-way and 2-position shut-off valves release the downstream pressure when in the closed position. They can also be locked in the closed position for safe maintenance.
Isolate a part of the network
Ball valves are used to isolate a part of the system for maintenance purposes. However, they do not necessarily prevent accidental start-ups, since they cannot be locked in the closed position.
Soft start valves control the supply of compressed air to the system in a progressive manner with an electrical signal. They prevent potential water hammers which can damage sensitive equipment such as regulators. When the electrical signal is cut off, the valve shuts off the compressed air supply and releases the pressure from the system. Soft start valves are installed upstream of an FRL combination unit and downstream of a safety exhaust ball valve.
Slide valves are ideal for machine entrances and smaller areas (e.g. cubicles). When the ring is slid to the "open" position, air flows through the valve to the application. When the ring is returned to the "closed" position, the supply is cut off and the downstream pressure is released through the exhaust ports, preventing the operation of the tool or machine. This makes it a safe and economical way to operate single-acting pneumatic cylinders, pneumatic clamps, and other pneumatic equipment.
Miniature 3-way valves with exhaust are ideal for machine entrances and smaller areas (e.g. cubicles). They are ideal for automation systems (pneumatic) and are used with plastic tubes. When closed, the 3-way miniature valve releases the residual pressure.
Piloted valves are ideal for ceiling installations as they allow the isolation of high sections of the air network without using a basket or a ladder. It allows the air supply to be opened and closed from the ground, quickly and safely. The user is also guaranteed safety by eliminating any risk related to working at a height. Some models can even be locked.
How to make your workstation ergonomic
Working in an ergonomic environment helps prevent injuries and accidents. This rule applies to all environments.
The main benefits of an ergonomic workstation:
- Reducing the stress of always being on the lookout or tripping over a hose on the floor
- Reduce musculoskeletal issues caused by repetitive movement, discomfort, fatigue, or heavy tools
- Reduce absences due to accidents
- Reduce errors during line production
- Increase the overall productivity of the company
Improving tool maneuverability
By improving the maneuverability of tools, you improve the performance and efficiency of your employees, while making them appreciate their work more because you make their lives easier. Your employees will thank you for it. Here are three solutions:
Coiled hoses offer freedom of movement and are therefore widely used in workshops. They stretch easily and return to their original position when the job is done. Each end has a swivel connection for better tool handling. The two ends are of different lengths: The longer end is equivalent to the length of the arm for ease of use.
Snubber hoses improve maneuverability, especially in tight areas. They help reduce wrist fatigue caused by repetitive motions and contribute to increased productivity in the workplace. They are installed between the air tool and the quick coupler. They increase the life of the quick coupler since they absorb vibration from the compressed air.
Swivel fittings and coupler plugs help reduce wrist fatigue. They come in handy in tight spaces, such as when using a sander in the furniture industry.
- They allow a 360° free rotation of ° at the base.
- They have an angle that goes from 30° to 90° in all directions depending on the model.
- They prevent kinking of the feeder hoses and thus increase the life of the hoses.
- They help prevent carpal tunnel syndrome.
Reduce physical effort
Here are some solutions to reduce the physical effort required by employees when performing their work.
Automatic hose reels make it easy to store air hoses to have them ready to use at all times. Automatic hose reels allow you to reel in hoses effortlessly. Plus, when hoses are in reels, you can pull out only the length you need. The wrist does not have to support the weight of the hose.
Some blow gun models have a gas handle, which makes them easy to use and protects the trigger from wear and tear while protecting your fingers. When choosing a blow gun, look for one that is lightweight and fits in the palm of your hand with a good grip, making it easier to handle.
Some air guns or sprayers have a handle that is aligned with the tube as if you were holding a ski pole vertically. Other air gun models have a shoulder handle to distribute the weight of the tool and direct the air stream and/or have an adjustable auxiliary handle that allows the 2-handed operation to hold the sprayer wand.
Tool balancers make pneumatic and electric tools "weightless" (0 gravity) by using a spring tension set to equal the weight of the tools. They can be suspended from a boom or track.
- They are ideal for assembly lines or work areas.
- They keep tools within easy reach. Tools suffer less damage by being suspended out of the way above the work surface.
- They reduce the number of movements made, thus promoting faster and more efficient work.
- They help reduce fatigue, resulting in greater productivity, fewer errors, and fewer injuries.
- They help prevent accidental starts by keeping tools out of the way.
- Reduce the risk of accidental falls by keeping tools out of the way when not in use.
How to prevent tripping
Not only can an employee fall by stepping or tripping on an air hose and hitting whatever is around them, but they can also drop the tool connected to the hose. This can cause the tool or connection to break and damage whatever was hit in the process. Tangled, untied hoses are prone to premature wear because they are more exposed to their environment of dust, dirt, oil, and other chemicals.
Hose reels can be mounted on the ceiling, wall, floor, or under a worktable. This frees up the floor from hoses and allows for easy access to tools. They increase the efficiency of using a hose. See the article How to Choose a Hose Reel for Compressed Air to learn about the different options available to you.
- They help limit the risk of accidents.
- The risk of tools and fittings falling to the ground is greatly reduced, as is hose wear.
- They reduce maintenance and replacement costs for hoses and tools.
- It also prevents the risk of hose punctures that could cause dangerous whiplash injuries.
How to protect the air system from overpressure
Overpressure occurs when the pressure in the system is higher than the air demand of the tools and equipment. Each tool and piece of equipment has manufacturing specifications and requires a precise amount of air. When using a tool or equipment, you should never exceed the pressure recommended by the manufacturer. If you don’t you could face :
- A tank or equipment explosion
- Premature wear of tools and equipment
- Problems with the quality of finished products
- Projectiles
Tank and compressor safety valves are designed to protect compressed air distribution systems from overpressure. The pressure is pre-set at the factory to a non-alterable setting, in which case the safety valve releases the air in the system into the atmosphere.
The valves are manufactured in accordance with the safety valve standards of the "National Board of Boiler and Pressure Vessel Inspectors, Section ASME VIII." (RBQ B-1.1 r.6.1 - Section II) Many models have a Canadian Registration Number (CRN). And some stainless-steel models offer better corrosion resistance.
⚠️ Caution: You must test the safety valves annually by forcing them open manually. If you have never performed an annual test, you must change the valve 5 years from the date of service. A safety valve for tanks and compressors must in any case be changed every 10 years. ⚠️
How to dispose of condensates
Water and contaminants cause pneumatic equipment failure and promote bacterial growth in compressed air piping. Removing and treating condensate and contaminants safely and effectively while ensuring clean, dry air quality is necessary.
Most compressors are oil lubricated. Therefore, some of the air leaving the system has oil in it from the compressor. The concentration of oil in the air is calculated in parts per million (ppm) and varies from one compressor to another. For example, a reciprocating compressor emits an average of 7 to 10 ppm, while other types of lubricated compressors can emit more than 25 ppm. A typical compressor operating at 100 SCFM for 35 hours with an oil concentration of 25 ppm introduces 240 ml of oil into the compressed air system. The oil concentration only increases as the compressor wears out.
The water-oil separator is installed at the end of the condensate drain line and allows for the environmentally friendly disposal of wastewater. Its role is to collect the condensate from the compressor, filters, traps, and refrigeration air dryer by using advanced filtration technology with polypropylene adsorbents. The condensate passes through a primary filter, which depressurizes it and traps solid particles. The wastewater then passes through the filtration media which adsorbs the oil. Following this treatment, the oil concentration at the separator outlet is less than 5 ppm, which respects environmental standards for condensate discharge. The volume of water collected is up to 99.5% clean and the small amount of residual oil, 5 mg/L, can be legally discharged to the sewer. When the filtration media is saturated, the maintenance indicator shows that it must be replaced.
Environmental standards prohibit the discharge of wastewater and oil collected from compressed air systems onto land or into bodies of water. In addition, the Council of Ministers of the Environment (CCME) has issued a guideline, setting the allowable concentration of mineral oil and grease in water discharged to the sewer at 15 mg/L (Ref. PN1422). Most Canadian municipalities follow the CCME guidelines. Failure to comply can result in significant penalties, such as fines and clean-up costs of several thousand dollars, as well as a public announcement of the violation through a press release.
12 safety rules to remember
As a summary of this article, we have listed the most important safety rules. Download a copy of the detailed 12 Safety Rules poster and print copies to place in strategic locations in your workplace.
Links of interest
- Canadian Centre for Occupational Health and Safety (CCOHS) ↗
- Canadian Government ↗
- Quebec Government ↗
- Healthy Hearing. Top five occupations causing hearing loss, April 21, 2016 ↗
- Canadian Occupational Safety. WSIB asking workers ‘How old are your ears?, January 27, 2017↗
- Lobe. Reasons for consultation? What is occupational deafness? 2020. . ↗
- Occupational Safety and Health Administration (OSHA) ↗